TS-BASE 受発注
2024.07.24
誤出荷とは?発生する原因と影響、基本的な対策
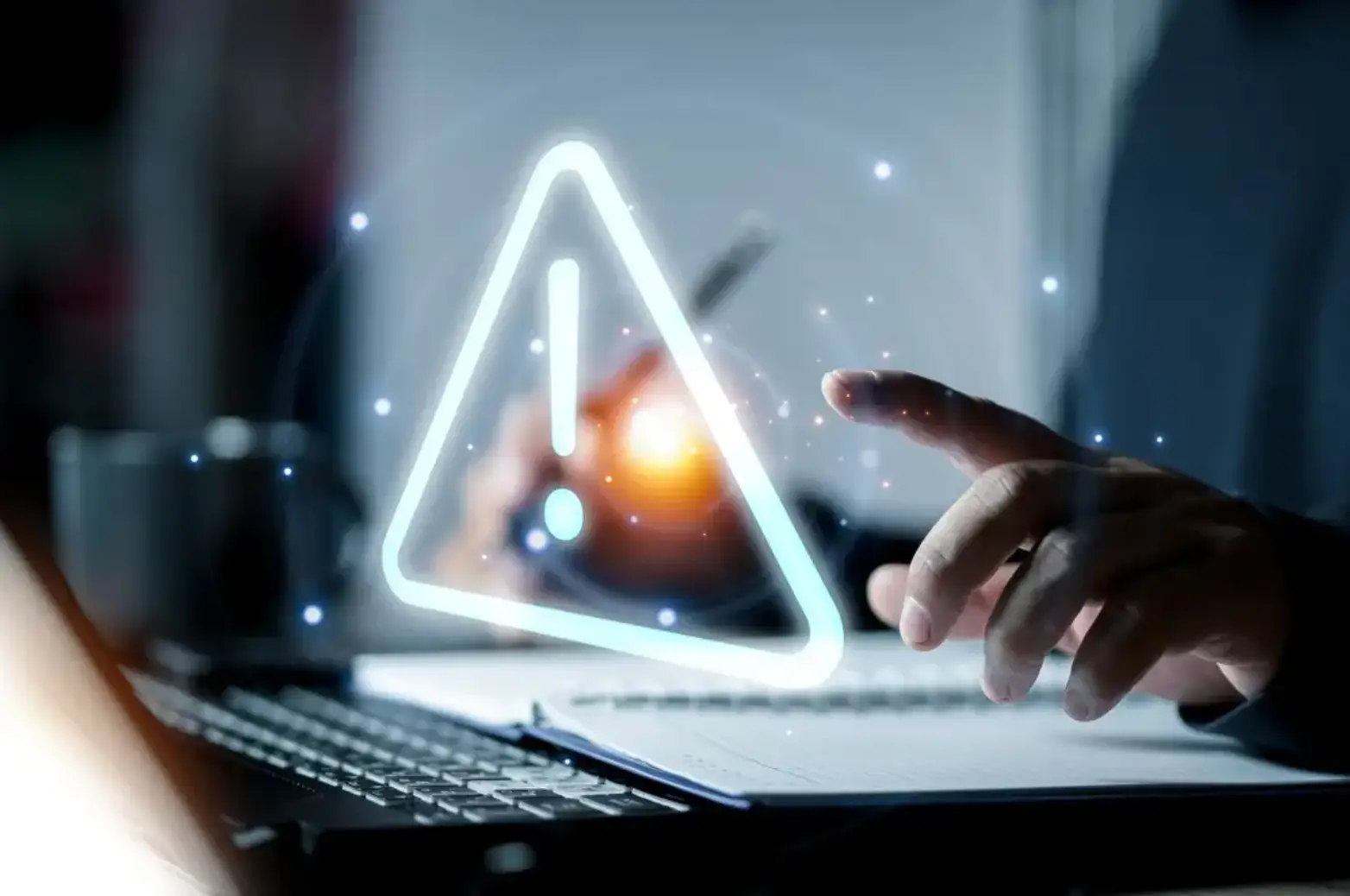
誤出荷は顧客満足度の低下や返品・再発送によるコスト増加など、企業にとって大きな影響を及ぼします。
この記事では誤出荷が発生する原因とそれによる影響、そして基本的な対策について詳しく解説します。
目次
誤出荷とは?
誤出荷とは、物流業務において誤った商品が出荷されることです。顧客満足度の低下やコスト増加につながるため、物流業務において重大な問題となります。
誤出荷によくあるケースを挙げます。
- 商品違い:顧客が注文した商品とは異なる商品が出荷される。
- 数量違い:注文数と出荷数が一致しない。多すぎる、または少なすぎる商品が送られる。
- 誤配送:正しい商品だが誤った配送先に送られる。
- 破損商品:出荷時に商品が破損している状態で送られる。
- 梱包ミス:注文内容と異なる梱包がされる、あるいは梱包が不十分で商品が破損する。
誤出荷が発生する主な原因
なぜ誤出荷が発生してしまうのでしょうか。考えられる主な原因をまとめました。
- ピッキングミス:倉庫内で商品を取り出す(ピッキング)際に、誤った商品や数量が選ばれるミスです。商品の識別が難しい場合や、ラベルやバーコードが不明瞭であったり、従業員の注意不足などが原因で発生します。
- パッキングミス:ピッキングされた商品を梱包する(パッキング)際に、誤った商品や数量が箱詰めされるミスです。商品の混入、梱包リストの確認不足、パッキング手順が徹底されていないことなどが原因で発生します。
- ラベル貼りミス:正しい商品が梱包されていても、誤ったラベルが貼られることで間違った配送先に送られるミスです。ラベルプリンターの設定ミス、ラベルの取り違え、手動でのラベル貼りの際の確認不足などが原因で発生します。
- システム入力ミス:注文情報の入力や確認において、誤った情報がシステムに登録されるミスです。データ入力時のヒューマンエラー、システムのバグなどが原因で発生します。
- 在庫管理ミス:在庫システムと実際の在庫状況が一致せず、誤った商品が出荷されるミスです。在庫システムの更新遅延、棚卸しのミス、商品移動の記録不備などが原因で発生します。
- 教育・トレーニング不足:従業員が業務手順や使用するシステムについて十分に理解していないことによるミスです。新人教育の不足、定期的な研修の欠如、マニュアルの不備などが原因で発生します。
- コミュニケーションの欠如:チーム内や部署間の情報共有が不十分であるために発生するミスです。業務連絡の遅延、情報共有ツールの不備、または部門間の連携不足などが原因で発生します。
- 作業環境の問題:作業環境が不適切であるために発生するミスです。倉庫内の照明の不足、作業スペースの狭さ、温度や湿度の管理不足などが原因で発生します。
誤出荷が引き起こす影響
誤出荷が起きると自社にとってマイナスの影響が発生します。具体的にどのような影響が考えられるのか、その例を紹介します。
- 顧客満足度の低下:誤出荷が発生すると、顧客に対して正しい商品が届かず、不満や不信感を抱かせることになります。これが続くと、顧客満足度が低下し、リピーターの減少や悪評の拡散につながる可能性があるでしょう。
- 返品・交換コストの増加:誤出荷が発生すると、返品や交換の対応が必要になります。この対応には追加の運送費用、再梱包費用、人件費などが発生するため、コスト面での負担が増加します。
- 在庫管理の混乱:誤出荷が頻発すると、在庫管理システムと実際の在庫状況にズレが生じ、在庫管理が混乱する可能性があります。在庫数の誤認識や不正確な在庫情報は、さらなる誤出荷や欠品を引き起こす原因となるでしょう。
- ブランドイメージの損傷:誤出荷が頻繁に発生すると、企業の信頼性やブランドイメージが損なわれます。顧客が企業を信頼しなくなり、他の競合他社へ流れる可能性が高まるでしょう。
- 業務効率の低下:誤出荷の対応に追われることで、本来の業務にかける時間やリソースが削られ、全体的な業務効率が低下します。また従業員は追加の対応業務やクレーム対応に追われ、ストレスが増加し、従業員の士気が低下。さらなる業務ミスが発生しやすくなります。
- 売上の減少:誤出荷により顧客満足度が低下し、リピーターが減少することで、売上が減少します。また、返品や交換によるコスト増加も利益率の低下に直結するでしょう。
誤出荷を防ぐための基本的な対策
誤出荷は顧客満足度の低下や企業の売上減少、業務の非効率化などを招く要因になります。可能な限り誤出荷をゼロにし、円滑に業務を進められるように対策を行うべきです。では具体的にどのような対策ができるのか紹介します。
バーコードシステムの導入
商品のピッキングから出荷までの全工程でバーコードを活用することで、正確な商品管理が可能となります。バーコードリーダーを使って商品情報を読み取り、誤出荷を防ぎます。
ピッキングリストの精度向上
正確なピッキングリストを作成し、ピッキング作業時に商品の品番や数量を確実に確認することで、誤出荷のリスクを減らします。またリストを定期的に見直し、最新情報を反映させましょう。
ピッキング業務についてこちらの記事でも解説しているので、あわせてご覧ください。
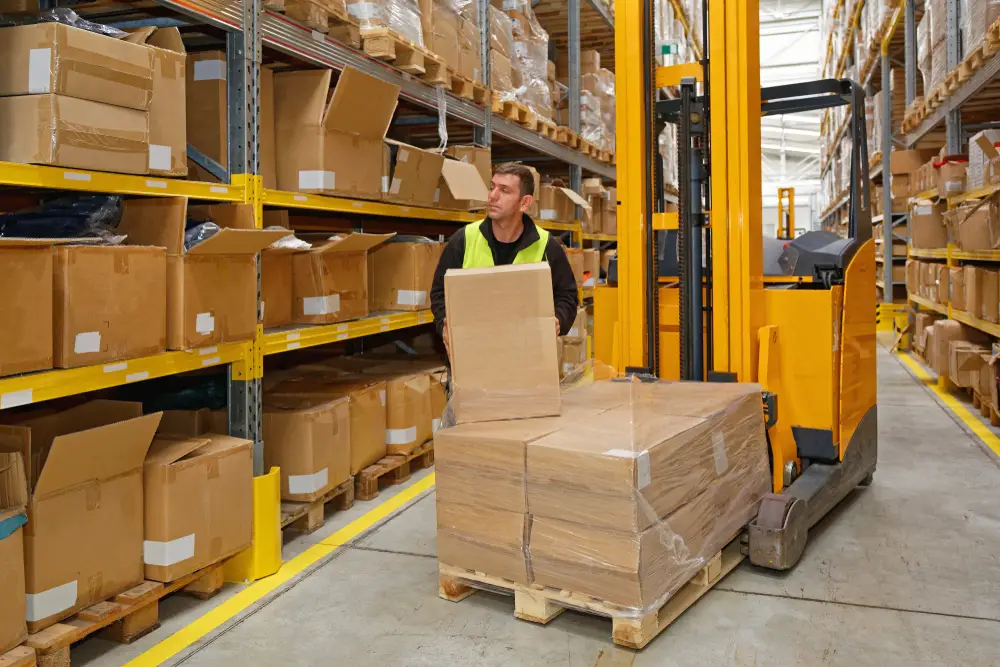
ダブルチェック体制の導入
ピッキングやパッキングの際に、複数の担当者によるダブルチェックを行うことで、ヒューマンエラーを減らします。二重の確認プロセスを経ることで、誤出荷の発生を未然に防げる確率が高まるでしょう。
従業員の教育とトレーニング
従業員に対して、正確なピッキング・パッキングの方法や、誤出荷防止の重要性について定期的な教育とトレーニングを実施します。また作業手順に変更があった場合は担当者全員に共有し、手順変更によるミスを可能な限り防ぎましょう。
システムの自動化と最適化
受発注管理システムや倉庫管理システム(WMS)を導入し、業務の自動化と最適化を図ります。システムが自動で在庫情報を管理し、適切なピッキングリストを生成することで、誤出荷を防ぎます。手動で行うよりもシステムを用いて自動化したほうがミスを減らせるでしょう。
受発注管理システム・倉庫管理システムについては以下の記事で解説しています。
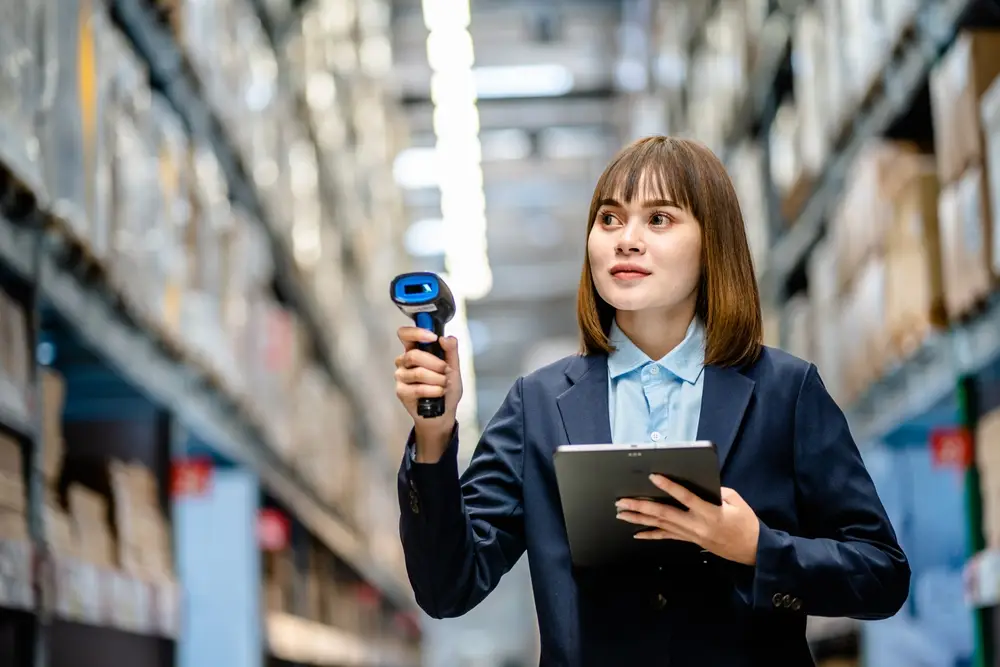
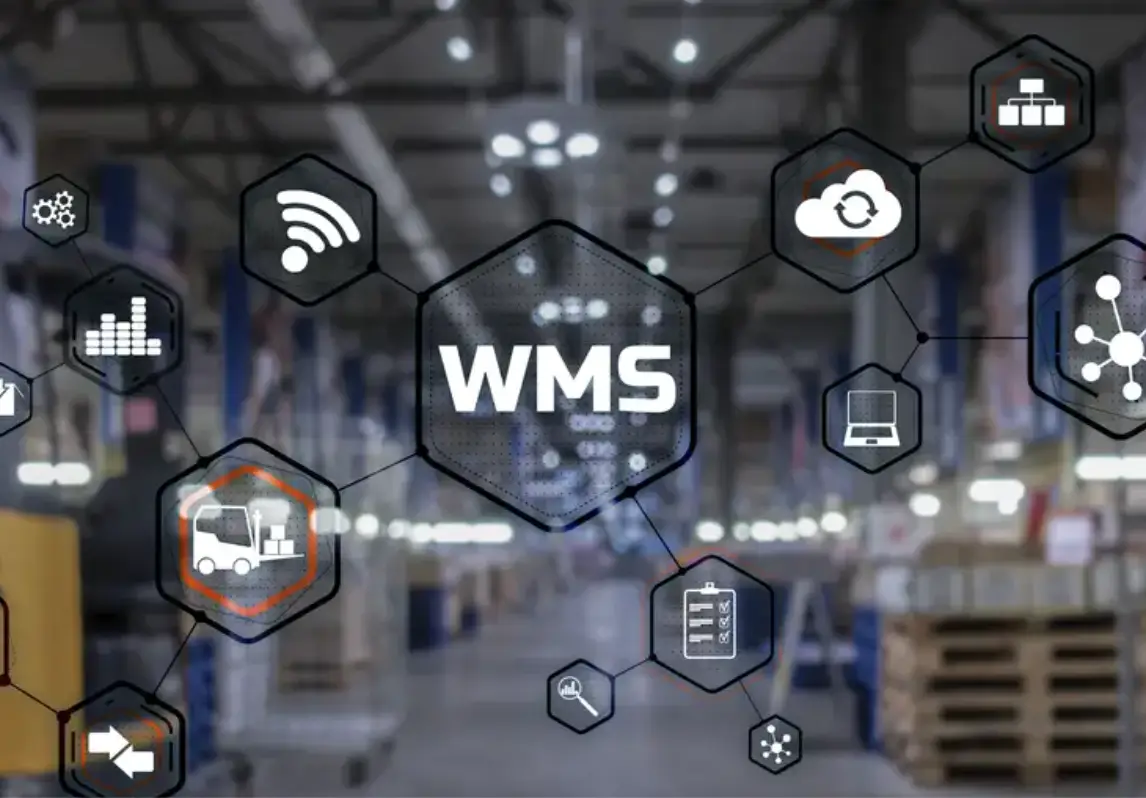
適切なラベル表示
商品や梱包箱に適切なラベルを貼付し、内容物や出荷先を明示します。ラベルの内容をピッキングリストと照合することで、出荷ミスを防ぎます。
業務プロセスの定期的な見直し
業務プロセスを定期的に見直し、改善点を特定します。プロセスの効率化や作業手順の見直しを行い、誤出荷を防ぐための最適な方法を模索しましょう。特に誤出荷が頻発している場合は見直しが必須です。
環境整備
倉庫内の環境を整備し、商品の保管場所を明確にします。整理整頓された環境で作業を行うことで、ピッキングミスや出荷ミスを減らすことができるでしょう。
フィードバックシステムの導入
誤出荷が発生した場合、その原因を分析し、フィードバックを行うシステムを導入します。このようなシステムがあると従業員が過去のミスを学び、再発防止に努めることが可能です。
適正な人員配置
業務量に応じて適正な人員配置を行い、過剰な負担がかからないようにします。適切な労働環境を整えることで、従業員の集中力が維持され、ミスの発生を減らすことができるでしょう。明らかに人員が少ない部門はないか、従業員からの意見を参考に検討してみてください。
物流業務のアウトソーシングも方法の一つ
「物流業務を自社で行っているが、誤出荷が目立つ」などのお悩みを抱えているなら、物流業務をアウトソーシングすることもおすすめです。アウトソーシング先となる業者は物流業務に関する専門スキル・知識を保有し、最新の技術を備えているため、自社で行うよりも質の高い業務が期待できます。また物流業務をアウトソーシングすることで従業員の負担を軽減でき、業務過多によるミスを減らすことも可能です。
その他、物流業務をアウトソーシングするメリットや具体的な方法について、こちらの記事でまとめています。ぜひご覧ください。
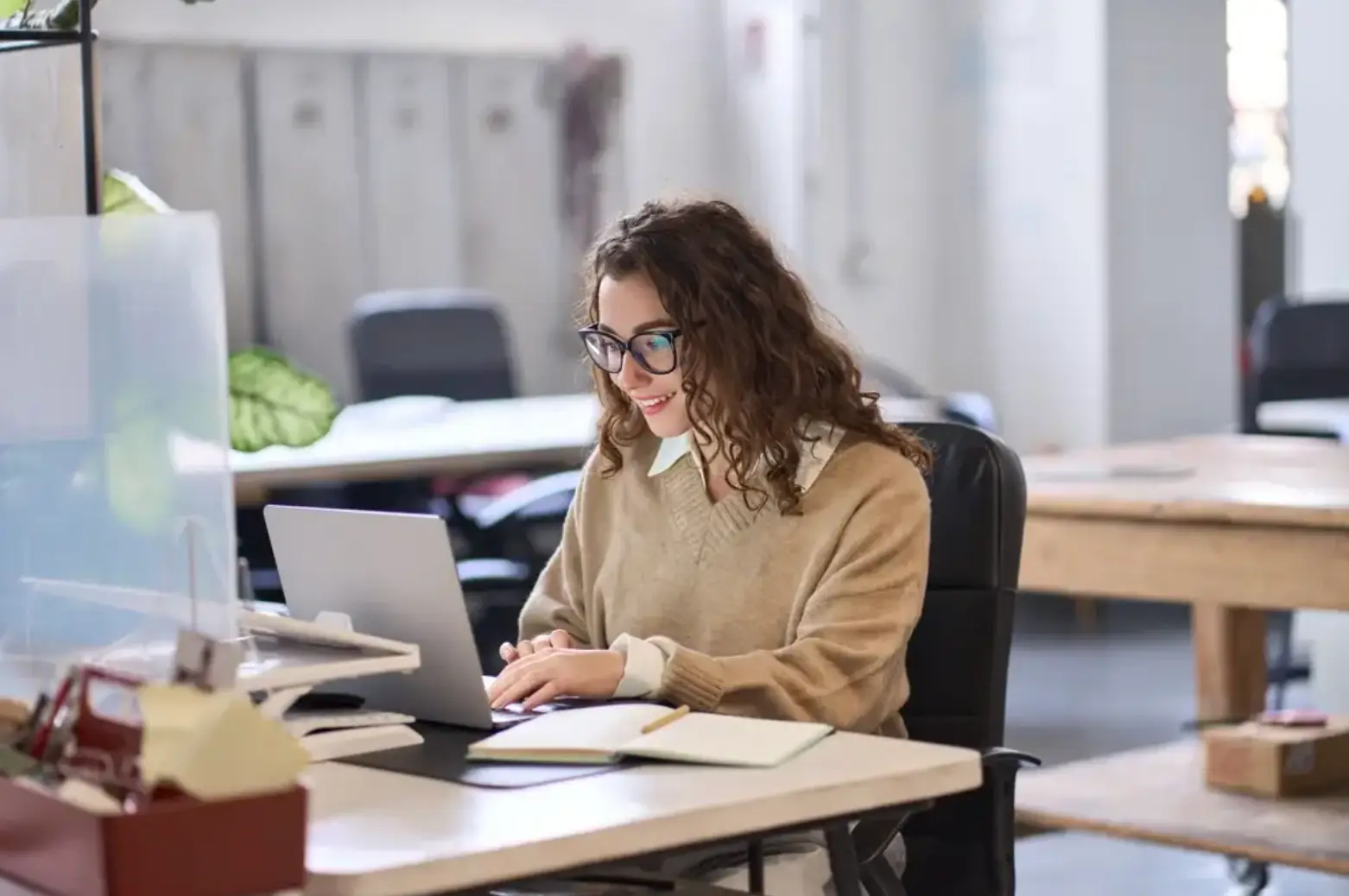
対策を行い誤出荷をなくそう
誤出荷は企業にとって避けたいトラブルの一つですが、適切な対策を講じることで、そのリスクを大幅に低減することが可能です。顧客満足度の向上とコスト削減のために、改めて自社の出荷プロセスを見直し、適切な対策を実施しましょう。
-
TS-BASE編集部さん
TS-BASEシリーズの促進を目指し活動しています。
導入をご検討の方は
こちらから
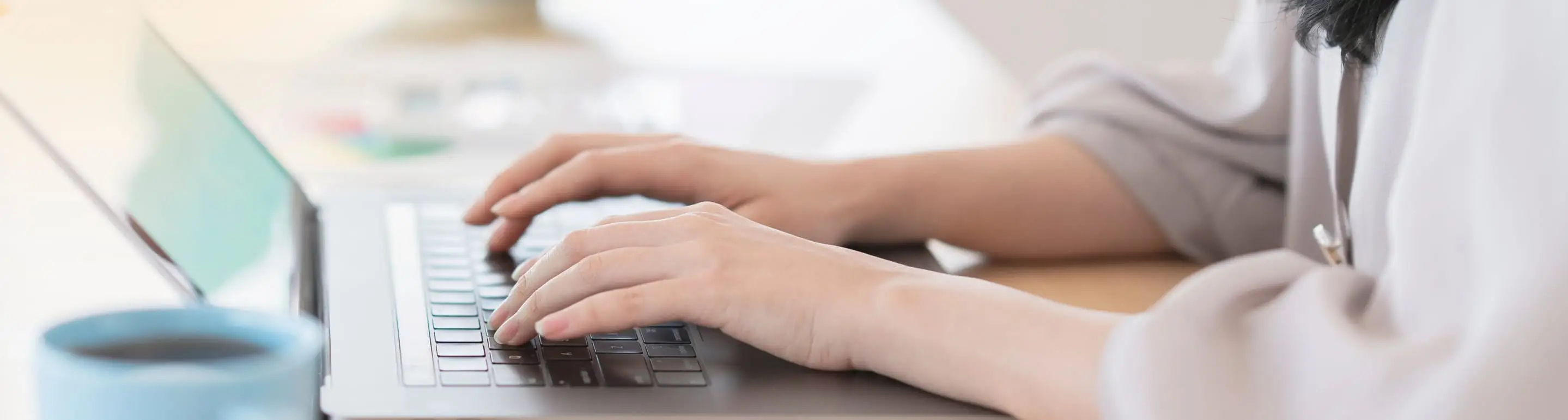
-
サービスの紹介資料や
お役立ち資料は
こちらから -
導入のご検討やその他ご相談は
こちらから